Pilot-Operated Pressure Relief Valves
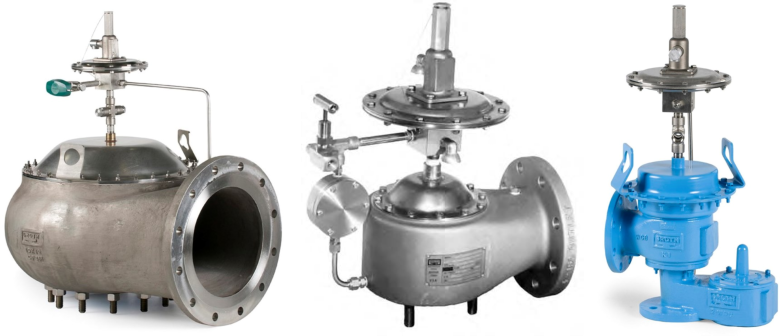
Pilot Operated Relief Valves serve the same primary purpose as pressure / vacuum relief valves, but with better performance characteristics than weight or spring loaded valves. Lower leakage and better flow performance make a pilot operated valve the solution when the focus is product conservation, expanded tank working band, and reduced fugitive emissions. A pilot operated relief valve provides the maximum available leakage control technology as specified in the Clean Air Act of 1990.
Emergency Relief Valve – Pilot Operated Model 2500A :
Designed to provide emergency relief capacity beyond that furnished by the normal operating pressure relief valve on the tank. The valve protects the tank against rupture or explosion that could result from excessive internal pressures caused by an external fire, etc. Model 2500A is designed to be self-closing. As excessive pressure builds up, Model 2500A relieves, then reseats when overpressure has been dissipated.
Key Features:
- DOCUMENTED COMPLIANCE TO EPA’S METHOD 21 TESTING (<500 PPM LEAKAGE AT 90% OF SET PRESSURE)
- ANSI 150# AND API 650 DRILLING
- DERAKANE, FURAN, CARBON STEEL,316 SS, AND OTHER BODY MATERIALS AVAILABLE
- FULL LIFT BY 20% OVERPRESSURE
- TRIM AVAILABLE IN 316 SS OR HASTELLOY C
- STANDARD FEP DIAPHRAGM
- PRESSURE SETTINGS 5 INWC TO 6 PSIG
1660A Pilot-Operated Relief Valve with Pipe-Away feature :
Used on liquid storage tanks and other process vessels or systems to prevent structural damage due to excess internal pressure or vacuum. The pilot-operated relief valve has two principal advantages over standard types of relief valves:
- it is bubble-tight to set pressure
- it is fully open at less than 10% above set pressure.
Key Features:
- SIZES 2″ THROUGH 12″
- PILOT OPERATED RELIEF VALVES 1660A
- FULL PIPE BORE SEAT NOZZLE
- STANDARD PRESSURE SETTINGS FROM 2.0 INWC TO 15 PSIG
- TEMPERATURE RANGE FROM -323° F TO 300° F
- DESIGNED FOR EASY MAINTENANCE
Contact us
If you would like to place an order or find out more, please email info@assentech.co.uk, call on +44 1726 844 707, or fill in a contact form here.