Go back to News
Breather vent performance: more testing needed
This article was published in the Mar 2022 edition of Valve World Magazine, the article can also be found here (article link)
By Ewart Cox Managing Director, Assentech Sales Limited
Breather vents in tank farms are regulated by two international standards. However, only a fraction of the manufacturers test to these standards. This in turn has led to leakages at tank farms.
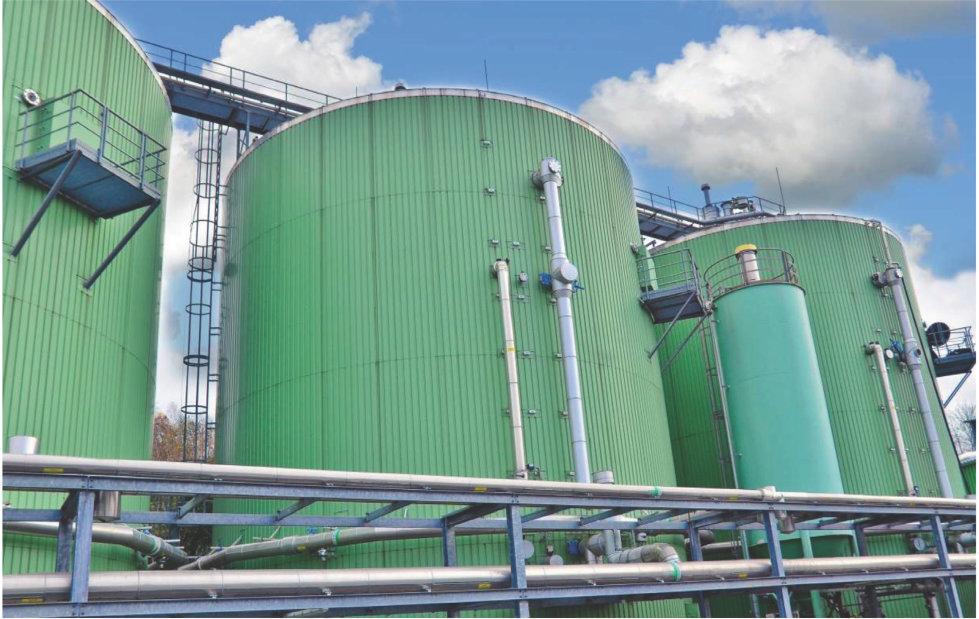
Most of the UK population live in towns and cities and often are close to industrial activity including bulk chemical/petrol storage and biogas generation. We are lucky to have
a legal infrastructure that ensures all UK operators follow strict safety and environmental guidelines intended to keep us safe but there is always room for improvement.
Our company passionately believes that huge reductions in emissions from tank farms can be achieved using the best available techniques and reference to international standards. The speed of change and increasing rate of adoption of new, cleaner technologies is literally breathtaking.
For example, Assentech has been developing techniques to measure and reduce emissions from tank farms for over a decade. The key is keeping volatile compounds inside the tanks but allowing them to breathe when required such as filling/emptying and fluctuations in temperature. At all other times, breather valves should remain closed with minimal leaks.
These valves have immense flow capacity so if not functioning or set correctly can leak hundreds of tons of invisible GWP emissions along with company profits into the atmosphere.
Win/win deal
Two international standards regulate the design, application and production of breather valves. These are ISO28300 and API2000. Both standards have specified maximum leak rates for all production vents, i.e. 0.014m3/h for vents up to 6”. The shame is that only two out of the 20 international manufacturers test to this standard. This ultimately has led to a huge problem with the majority of breather valves that are installed at facilities are not leak-tight and will allow huge volumes of vapour to release into the atmosphere. This is based on 25 years of experience in testing all manufacturer’s products. We would love to be proven otherwise, but unfortunately, I don’t see many companies coming forward to defend their position.
With over 1500 sites in the UK having more than 10 storage tanks with capacity ranging from 10 to 8000 tonnes of flammable or toxic liquid, the potential for leakage is immense. In a recent case study, we reduced a storage tank’s global warming potential from 161 tonnes of methane to just 185 kg per year by replacing just one 12” breather vent. By doing so we saved the customer £8k per year in lost methane per valve and an incalculable value to our environment. This was a true win/win deal.
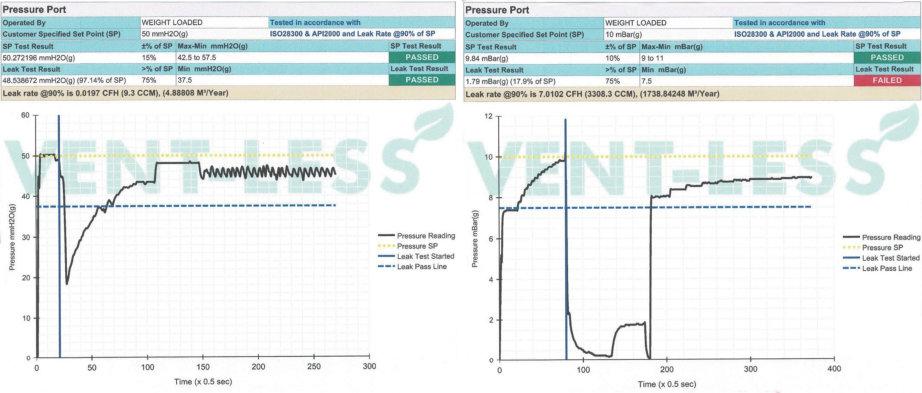
Challenging
It has taken us many years to develop an automated test bench to record these huge improvements using state-of-the-art artificial intelligence. Testing breather vents is surprisingly challenging when done manually. Because these tests are conducted
on modulating valves, the balance of flow control and measurement of change in pressure retained requires focus and detailed knowledge of the standards. Our automatic technology enables the machine to take pressure readings every 200 milliseconds referencing complex algorithms to make decisions on whether to increase or decrease flow.
This produces highly accurate and repeatable results in a fraction of the time taken by a manual test. The control system ac- actually has an artificial brain that instantly profiles the performance of a valve based on its reactions to changes inflow. It’s fascinating to see the bench produce results faster every time it tests the same valve. All decision making is built into the programming so there is no need for the technician to have detailed knowledge of the standards. Because the results cannot be influenced by the operator, the results are 100 per cent verified. This is a revolution in valve testing. Certificates are instantly transferrable to a smartphone by clicking on the QR code.
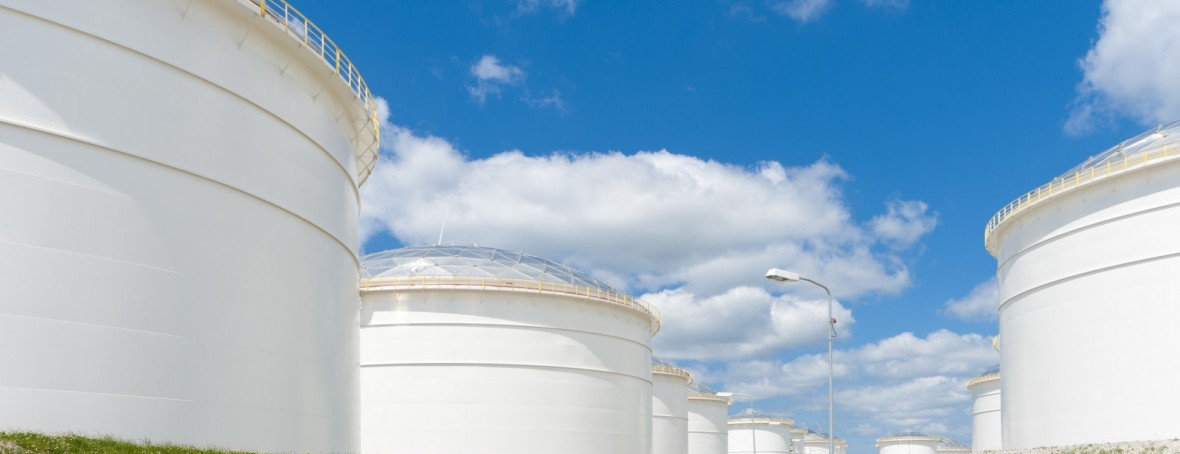
Significant benefit
Now, with the bench officially launched in August 2021, we are receiving a lot of interest, enquiries and orders from operators seeking to reduce emissions and meet ESG Environmental, Social and Governance) commitments. For example, we recently purchased two brand new valves for test R&D purposes. The bench is programmed to certify the leak rate over a 12-month period in addition to the standard parameters.
These valves were very different in terms of performance but looked very similar. One produced a leak rate equivalent to 1738m3/year and the other only leaked 4m3/year. That is a huge difference and choosing the right valve could make a significant benefit to both the operator’s profitability and the environment.
With the challenges we all face to reduce emissions as part of our journey to tackle climate change, we need collective energy and focus to ensure that operators adapt to these new challenges and are supported by the regulators.
The first step is to raise awareness of this huge industry problem and ask that you all take note of this huge issue. Our simple ad- vice is to ensure that end-users, regulators, and insurers insist on a valid individual leak test certificate on both vacuum and pressure ports for all the breather valves purchased, installed or serviced. It is a sobering thought that so many manufacturers of new valves installed onto £1m plus tank installations cannot produce evidence of individual testing prior to shipment. A typical tank valve has interchangeable pressure/vacuum pallets. So, how else can the buyer verify the valve has been assembled correctly?
Contact us
If you would like to place an order or find out more, please email info@assentech.co.uk, call on +44 1726 844 707, or fill in a contact form here.